PCS® Insights
Sharing Industry Knowledge, Lessons-Learned and Published Presentations
Pipeline Stress 101
Engineering for Non-Engineers
The world is in constant motion. Every day we rely on infrastructure to keep us safe as we accomplish our goals. In using this infrastructure, we are subjecting it to many stresses which it must be designed to handle. If you do not notice the pipelines around you, they are operating well. The gas stove will cook your food. The heat will kick on during winter. You can fill your tank at the gas station.
Pipelines are an extremely safe way to transport energy across the country. A barrel of crude oil or petroleum product shipped by pipeline reaches its destination safely more than 99.999% of the time. The reliability of this infrastructure is assured by careful design that takes many factors of its use and environment into account. Pipelines must be designed to withstand many stresses while safely transporting hydrocarbons for many years. A single failure at any point in the pipeline will shut a large section of the system and markets down, possibly causing serious safety concerns and economic consequences to operators and the general consumer. So what exactly are these stresses that a pipeline needs to be designed to withstand? PCS Engineering gives a glimpse into pipe stress, one of the many factors that go into designing a pipeline.
1. Internal Pressure from Compressed Fluids
The pipeline must contain the product flowing through it. No leaks. Inside, everything is at a very high pressure and wants to escape, pushing against the edge of the pipe walls. The pipe walls need to be strong enough to withstand that force and keep that pressure directed towards making the product flow through the line.
First, a proper pipe material must be chosen (e.g. one of many grades of steel). It must be strong enough to withstand the pressures. It also must not chemically react with the product being carried. Next the walls of the pipe must be thick enough (wall thickness, or “t” in the diagram above) to withstand the forces pushing against them. These forces are calculated based on the product flowing through the line (e.g. crude oil, natural gas, etc.) and the temperature and pressure range for which the pipeline is being designed. Another name for this internal pressure is Hoop Stress.
2. Thermal Expansion from Temperature Changes
Average changes in temperature over the year. Max and min vary based on depth-of-cover. (Source)

Pipe buckled from compression
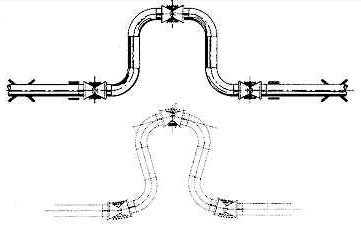
3. Material Irregularities are Sitting Targets
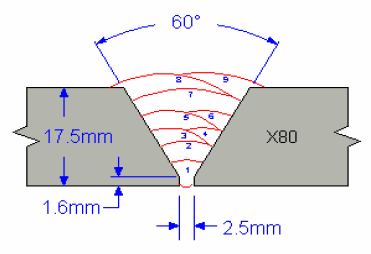
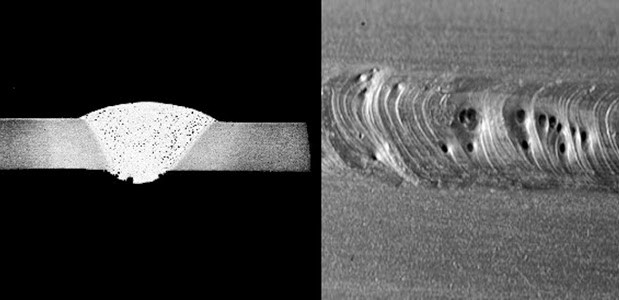
4. Heavy Loads – Soil, Trains, Buildings, etc.
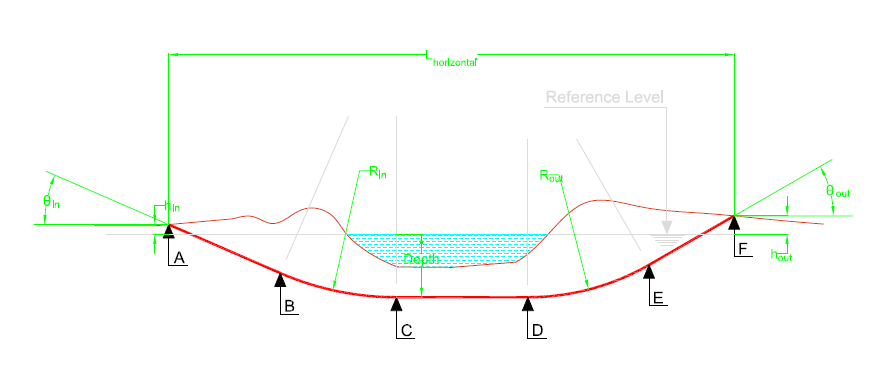
5. Bending Stress
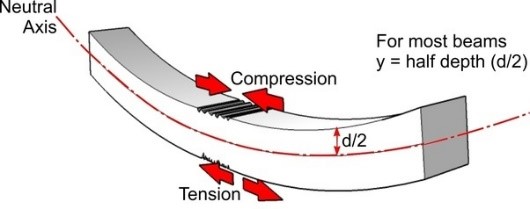
Example of a pipe bend. Each type of pipe has a maximum allowable bending radius (R in diagram) (Source)
Example of a Bending machine for Field Bends
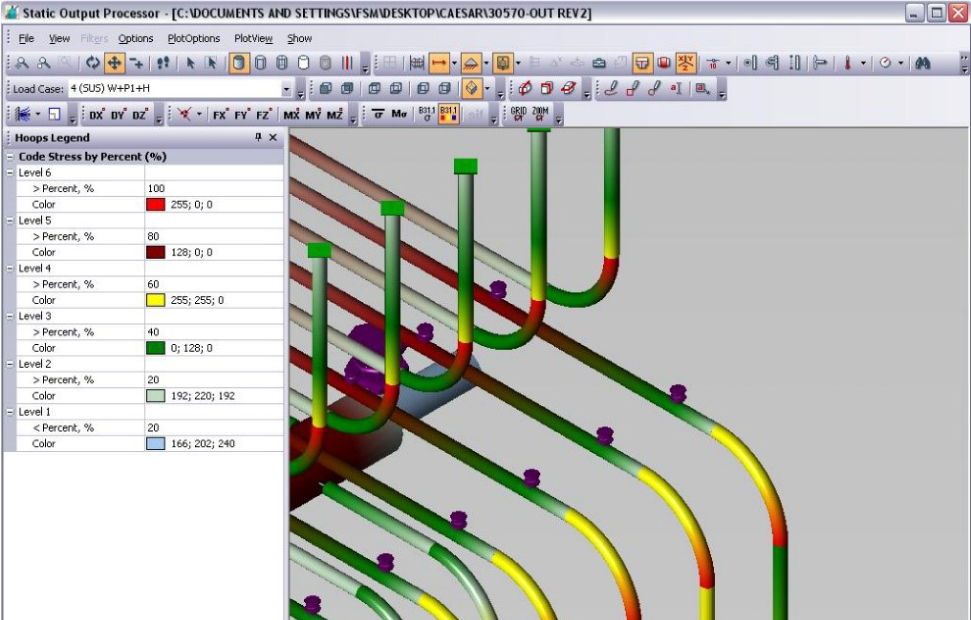
Article Details
Author: Zackery Breeland
Engineer
PCS® Metairie
More Information
Contact Us
We would appreciate any opportunity to assist you, and to connect you with the right person at PCS ® to address your needs and answer any questions.
Request Info Call Us 1-800-643-8306